- Customer Case Example 2025/03/28 UP
-
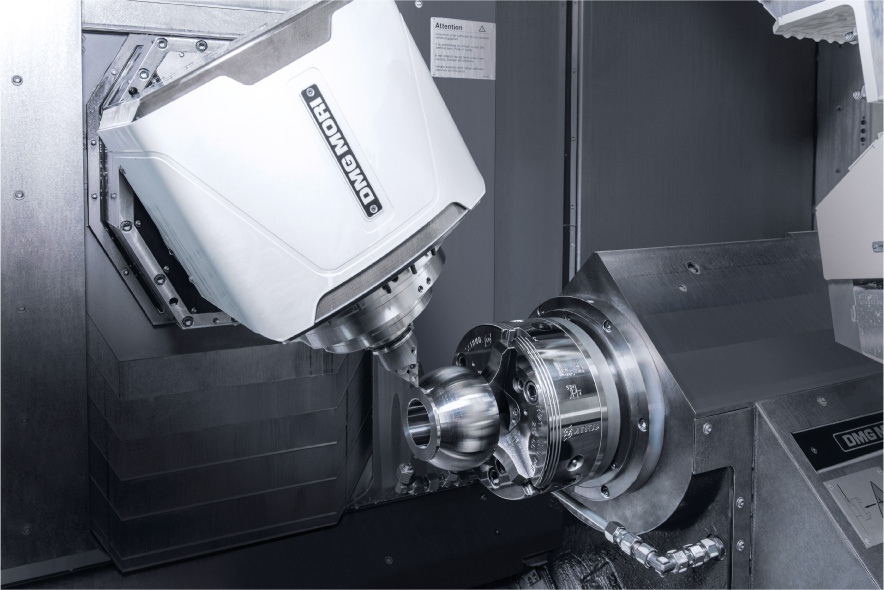
Kassel-based HÜBNER GmbH & Co. KG has its origins in a repair workshop for rubber products, which was established in 1946. In the 1950s, the company started to manufacture bellows for Deutsche Bahn carriages. HÜBNER also developed the first articulated buses together with Kassel company Henschel. HÜBNER now has 3,500 employees in production sites all over the world in Germany, Hungary, India, the USA and China, among others. The majority of the company's revenue nowadays comes from gangway systems connecting carriages in trains and buses. The range of services is now rounded off with the Material Solutions and Photonics divisions. The former develops demanding solutions made from elastomers, polyurethane and industrial textiles. HÜBNER Photonics specializes in the manufacture of pioneering lasers. In its production facility, HÜBNER places value on having a comprehensive manufacturing capability, especially in the machining area. The company has invested in machinery from DMG MORI repeatedly since 1988. It purchased its first automated manufacturing solution last year in the form of the CTX beta 1250 TC 4A with Robo2Go.
Complete gangway systems for buses and trains
Many people pass through gangway systems in trains, metros, trams and buses every day without paying particular attention to them. An “H” printed in one of the upper folds of the fabric often reveals that these connecting components were manufactured by HÜBNER. “We design the gangway systems in such a way that train and bus manufacturers can use them as complete components,” explains Patrick Wessel, production manager in the machine shop at the HÜBNER location in Kassel. Every train is different: “This means that practically every order is a new development, which takes place at the headquarters in Kassel, all the way to prototype manufacturing.” Because of the size of the gangway systems and the cross-section of the respective carriage, assembly great deal of manual work.
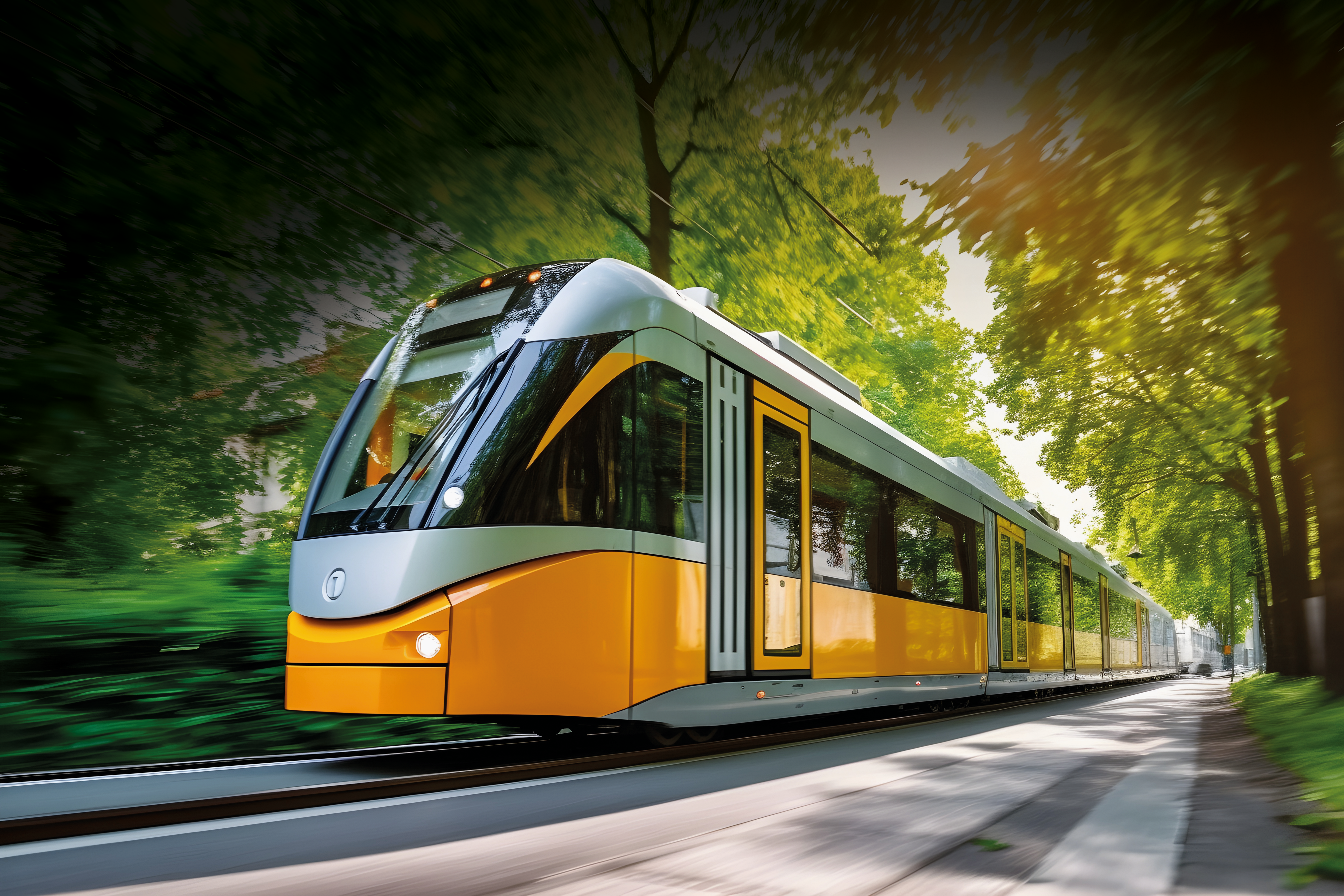
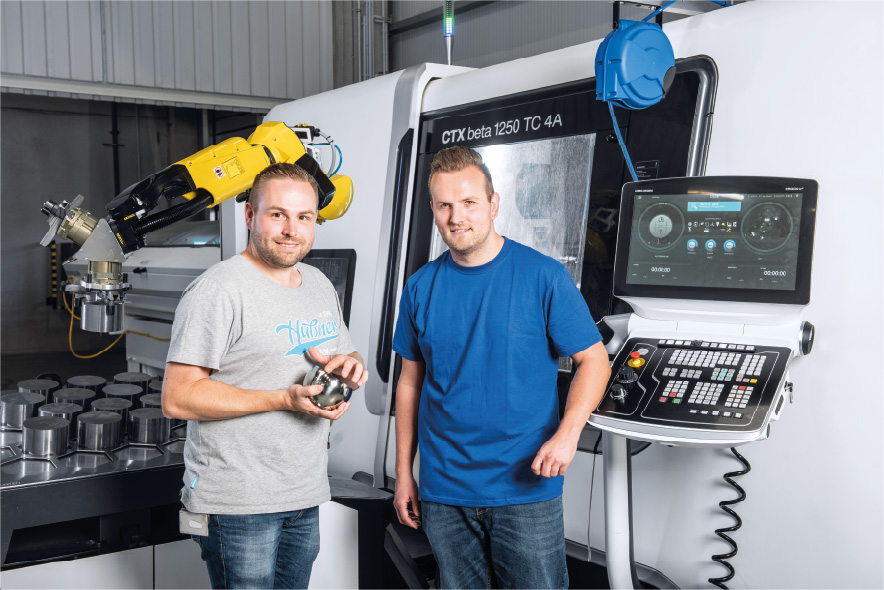
Thanks to the integration of turning and milling on one machine, we have reduced throughput times by 75%. The automation with the Robo2Go has also increased productivity by a further 30%.
Patrick Wessel, metal processing production manager (left)
Kevin Mönnich, CAD/CAM applications engineer (right)
HÜBNER GmbH & Co. KG
This content is for members only