- Tips on machining 2018/07/03 UP
-
Tips on machining vol. 21
2 ways to reduce boundary wear by managing tool path at roughing operation
【Turning】
- Tag
-
- Turning
- Roughing
Turning is a “continuous cutting operation” in which the cutting tool does not rotate, and its cutting edge maintains contact to the workpiece. This permanent contact of an insert to the workpiece has enormous negative impact on tool lifetime. “Boundary wear” arises at boundary areas where an insert and a workpiece have contact with each other.
Damage to the cutting tool becomes especially remarkable at boundaries, for example at “boundary to unmachined surface” when a cutting tool enters the workpiece for the first time, or at “boundary with coolant supply” and “boundary with cutting resistance” when a cutting tool reaches a certain cutting depth.
Moreover, as machining continues, there is a growing risk for “work hardening” where workpiece surface becomes hard through rubbing by an insert’s round tip, cutting force, or cutting heat. Work hardening is another factor that accelerates boundary wear.

Examples of boundary wear
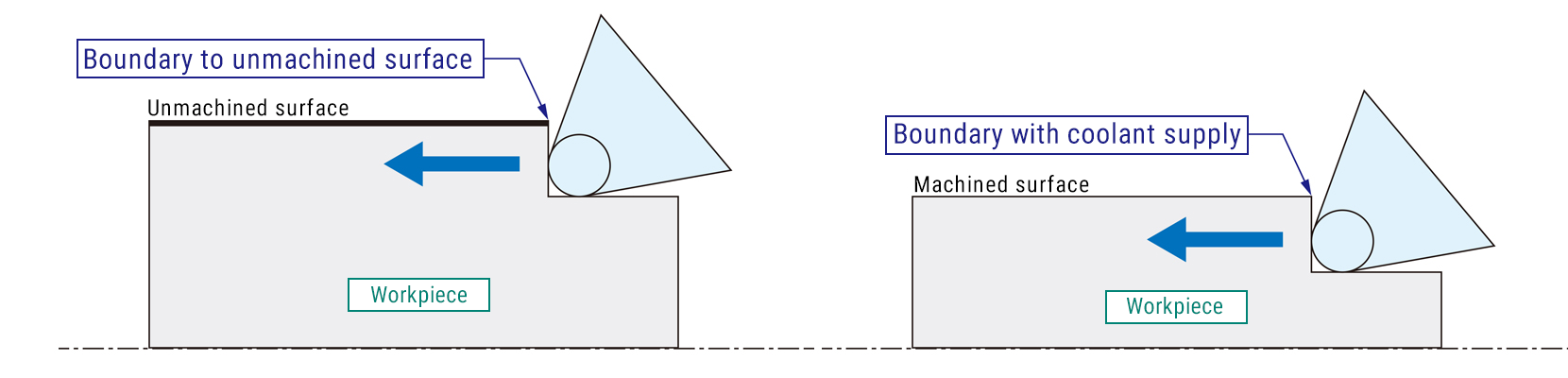
From left to right: “Boundary to unmachined surface”, “Boundary with coolant supply”
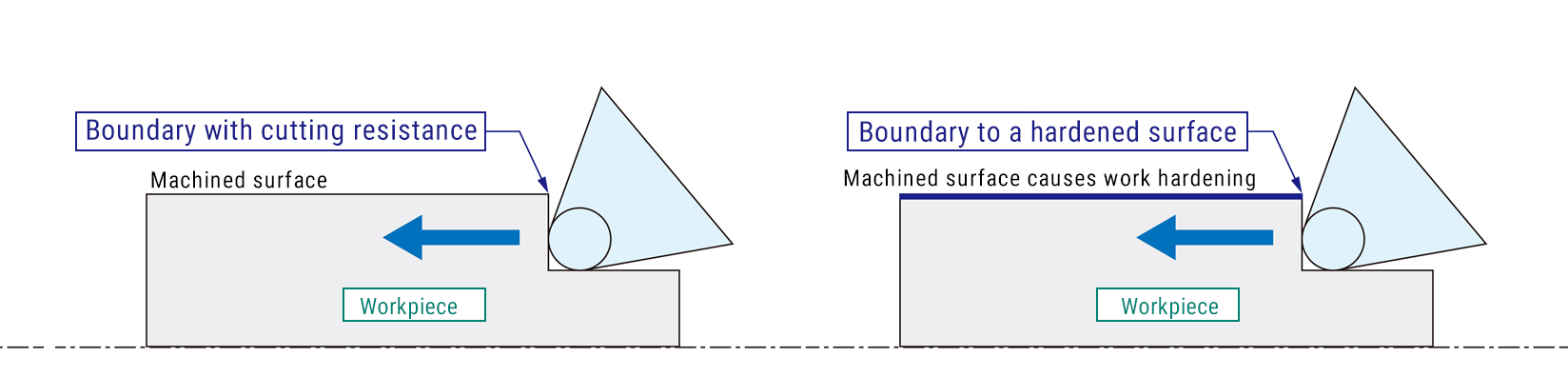
From left to right: “Boundary with cutting resistance”, “Boundary to a hardened surface”
When cutting distance increases and boundary wear progresses at an abnormally fast pace, the cutting edge becomes unusable, and the tool’s lifetime becomes extremely short. That is why it is important to avoid boundary wear when cutting hard material such as stainless steel or heat-treated material susceptible to work hardening.
There are 2 ways to avoid boundary wear: 1) By reducing load on cutting edge, and 2) By changing contact positions of cutting edge to workpiece surface.
This content is for members only