- Top page
- DMG MORI’s Technology
DMG MORI’s Technology
DMG MORI has consistently advanced its technology to meet evolving demands and significant societal changes through the development of innovative products and services. Our enduring mission remains focused on growth and contribution to the progress of society.
Research and Development
Innovative Products and Technology
to Benefit our Customers and Support Carbon Neutrality
Global Development Summit (GDS)
Global Development Summit (GDS)
Our R&D centers in Japan, Germany, the United States, Italy, and Poland accommodate approx. 1,300 development engineers. Once a year, they come together for the Global Development Summit (GDS) to discuss their latest projects face-to-face. During the GDS, future development plans are solidified through a plenary session, followed by specialized workshops where the latest market technologies and customer trends are discussed and shared. In 2020 and 2021, the GDS was held online. In November 2022, a hybrid-style was introduced and 100 engineers from Japan and oversees gathered in Tokyo while about 200 attended online. This marked the first face-to-face meeting in three years, albeit partially. This global sharing of experience and know-how greatly adds to DMG MORI's strong design and development.
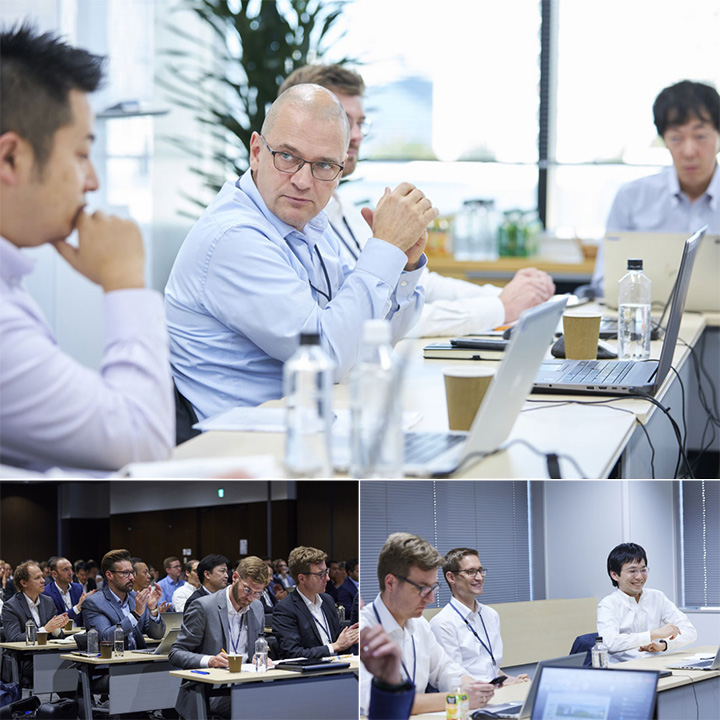
Nara Product Development Center (Nara PDC)
Nara Product Development Center (Nara PDC)
We opened the Nara Product Development Center (Nara PDC), the largest R&D center of DMG MORI with the primary mission of promoting digital transformation and cutting-edge technology. Nara PDC specializes in the development of next-generation communication technology, AI (Artificial Intelligence), DX technology with Digital Twins, next-generation mill-turn machines and peripheral equipment, and software. Moreover, Nara PDC houses a dedicated Development Experiment Center to conduct innovative experiments on machine tools, peripherals, and control units in close collaboration with universities and other companies.
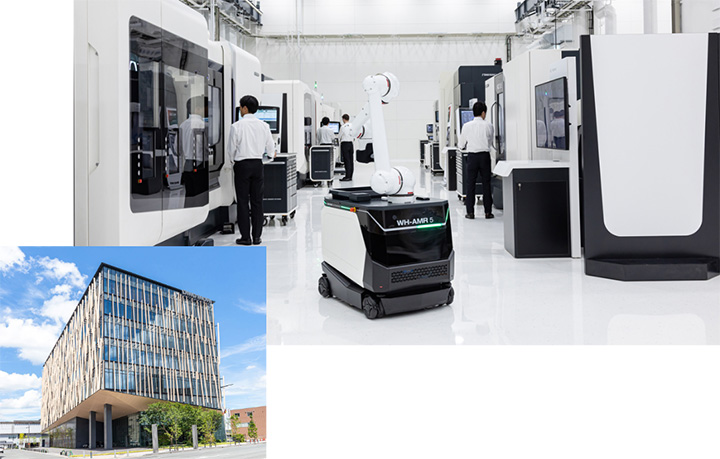
Sensing & Measurement
Sensing & Measurement
Measuring solutions are important for achieving high-precision machining. First, we developed the “Tool Visualizer” for automatic non-contact measurement of the tool shape directly on the machine tool. This not only enables high-precision tool compensation but also ensures the reliable detection of tool abnormalities to promote automation. In addition, we offer a non-contact on-machine measurement system that uses a laser scanner to measure the shape of workpieces after machining. This eliminates the need to load the workpiece onto a dedicated measuring device, which reduces the workload of operators and shortens the measuring lead time by 50%.
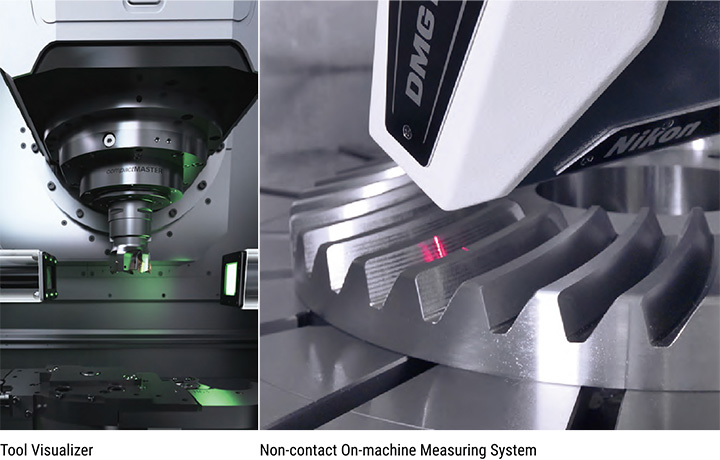
Pursuing Precision with Environmental Responsibility
Our fundamental principle is the development of machine tools that offer enhanced machining accuracy while minimizing their environmental footprint. As an example, in December 2022, we developed the NHX 10000 μPrecision, a large horizontal machining center that combines high rigidity and high precision with a volumetric accuracy of 15 μm or less. This model enables the high-precision machining of large workpieces utilized in industries such as construction machinery, aerospace, die & mold, automotive, and energy. Importantly, the NHX 10000 µPrecision contributes to reducing our customers' environmental impact by consuming less power compared to conventional machines.
DMG MORI will continue to promote Green Transformation through the development of green products that align with the evolving needs of precision machining.
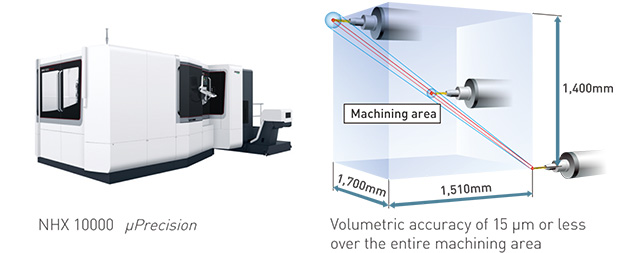
AM Technology for Process Integration, Carbon Neutrality and a Circular Economy
The Additive Manufacturing (AM) industry has made remarkable progress since its core technology was first patented in 1986. Initially recognized for rapid prototyping, its utility has progressively shifted toward functional prototyping. Subsequently, AM has gained prominence across diverse industries as a transformative approach to manufacturing, offering innovative functionality. Beyond its capacity to create components from scratch, AM serves as a valuable tool for repair and maintenance, significantly reducing waste and energy consumption.
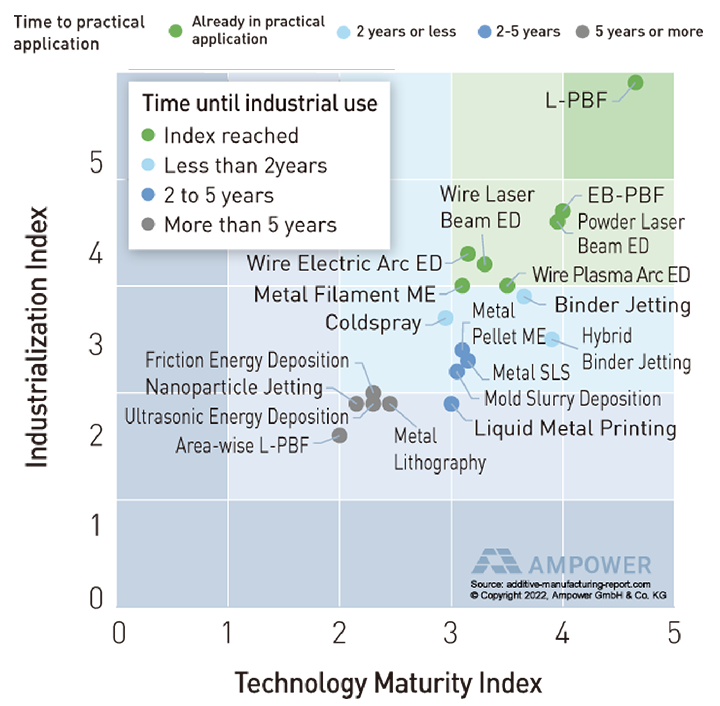
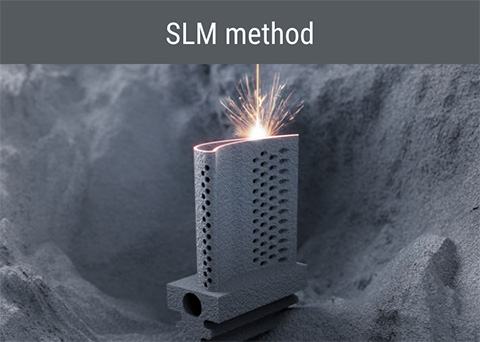
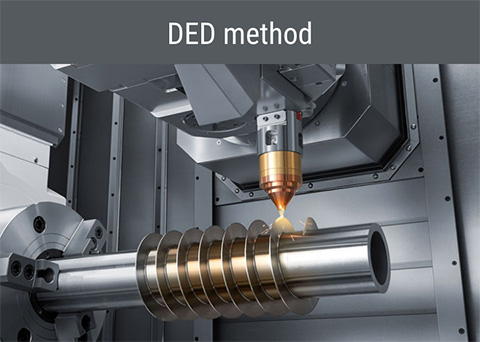
*Based to AMPOWER Report 2021 for the relationship between the level of industrialization and maturity of technology.
■ Our Global Order Intake from Additive Manufacturing
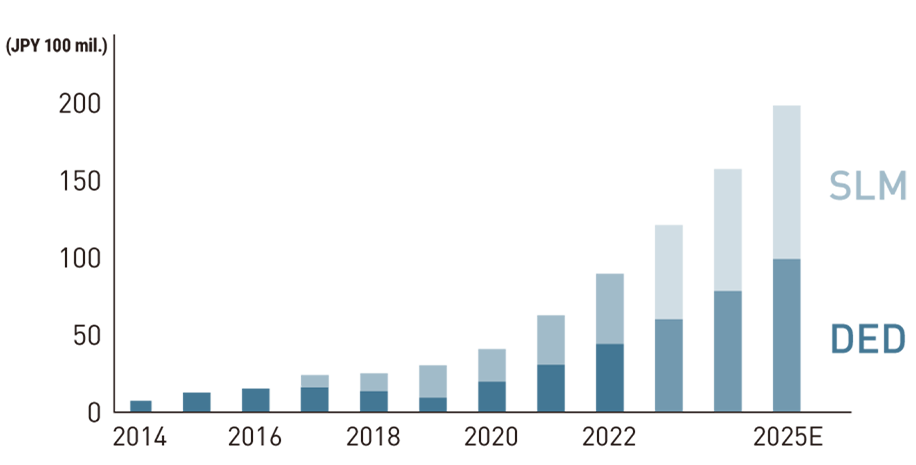
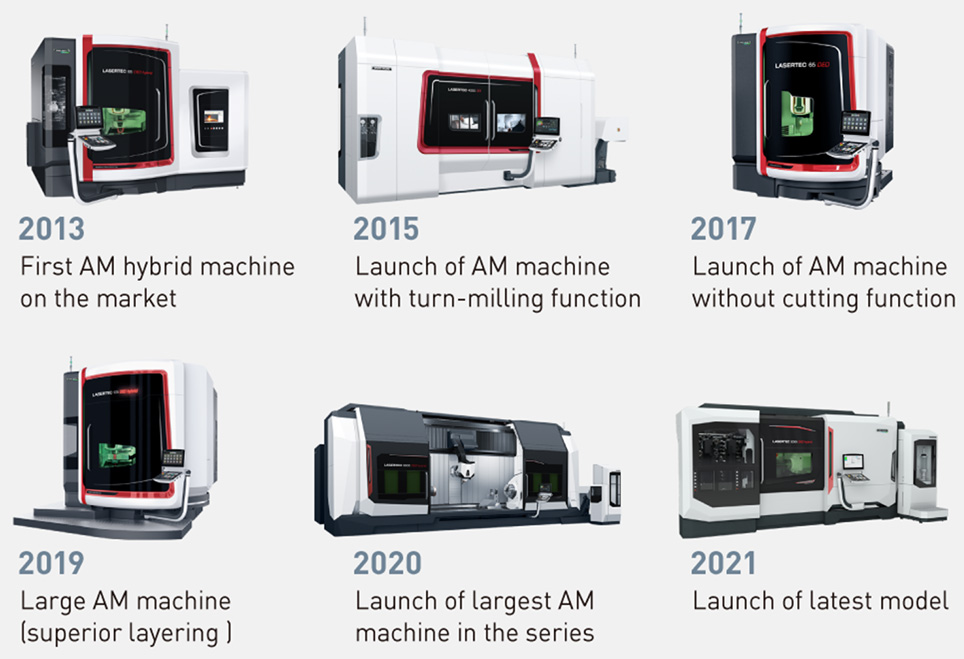
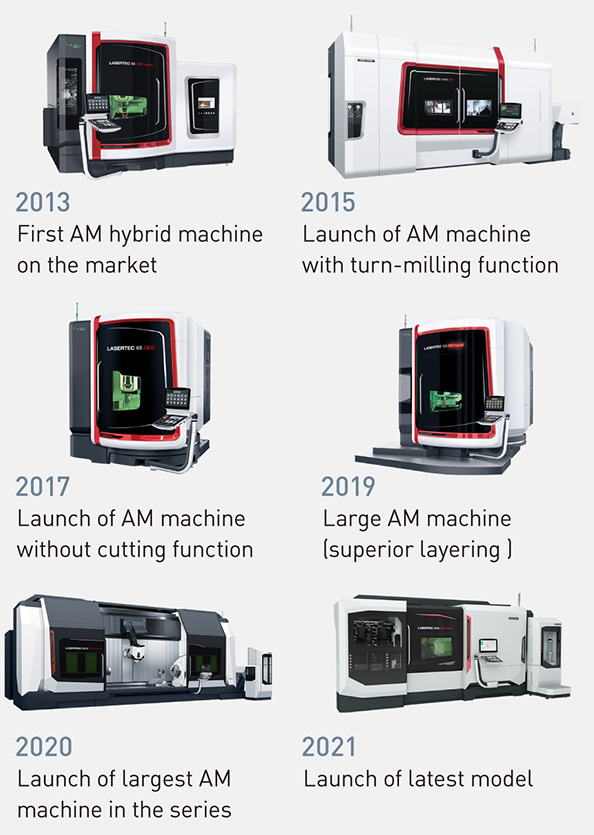
Production
Striving for Superior Quality, Reliable Supply, and Reduced CO2 Emissions
In-house Production of Key Components
In-house Production of Key Components
At DMG MORI, we prioritize in-house production of key components for the purpose of not only improving quality and shortening delivery times, but also shortening product development time and ensuring a stable supply. For ball screws and ATCs, our spindle factory is instrumental in overseeing the entire production process, from machining to assembly and inspection. We will continue to expand our in-house production in Japan, Germany, and other parts of the world.
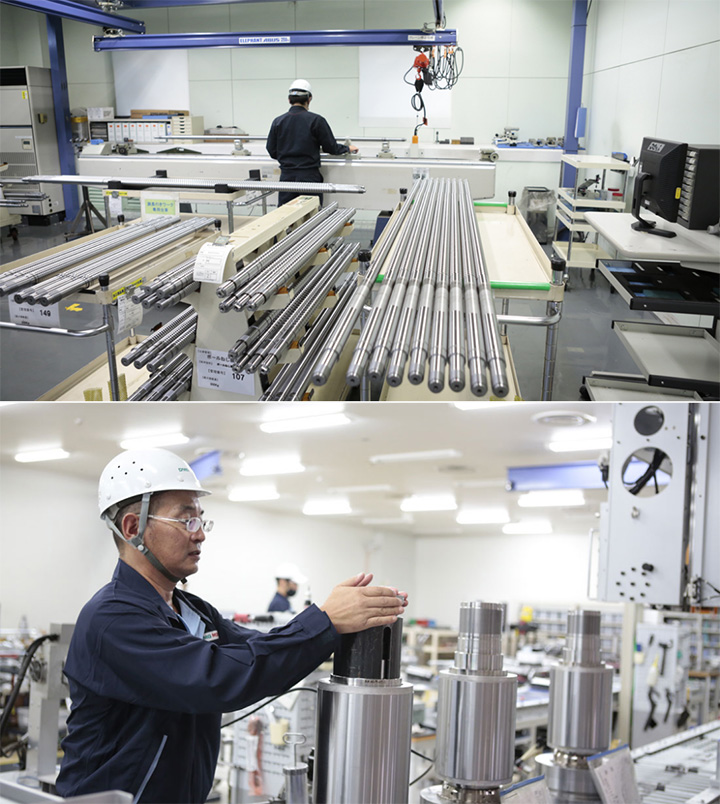
Introducing New High-Performance Spindles:
compactMASTER and turnMASTER
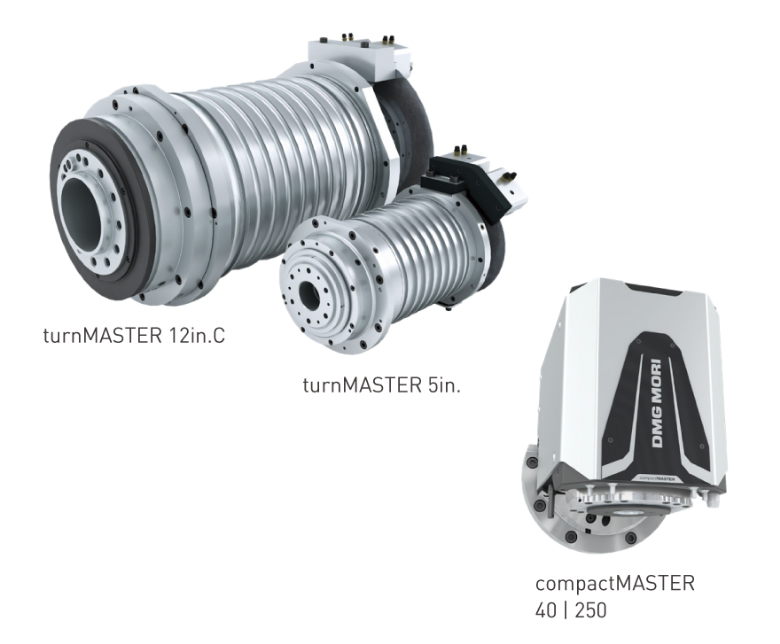
In June 2022, DMG MORI released two new spindles. The first is "compactMASTER 40 | 250", a turn-mill spindle known for its compact design with just 250mm in length. Despite its small size, it delivers impressive power and boasts a maximum rotation speed of 42,000 min-1. The second innovation is the "turnMASTER 5in.", a high-precision, high-performance spindle designed for turning centers and mill-turn centers.
In February 2023, DMG MORI launched the high-performance turning spindle “turnMASTER 12in.C”, which is about 18% smaller than the conventional model and can hold a chuck as large as 12 inches on a small machine tool. Since DMG MORI manufactures key components in-house, we are able to develop and build a variety of spindles. In addition, we offer a 3-year warranty period for spindles as a proof of quality.
DMG MORI-made machine tools are equipped with high-speed, high-performance spindles and manufactured under carbon-neutral conditions, thereby contributing not only to higher productivity but also to reduced CO2 emissions and environmentally friendly production sites.
Digital Transformation in Production – TULIP Across All Global Manufacturing Sites
Digital Transformation in Production – TULIP Across All Global Manufacturing Sites
DMG MORI has introduced TULIP at all its main production sites. TULIP is a platform that enables shop floor personnel to easily create various applications for work instructions, quality control, equipment monitoring, and data linkage with other systems such as Manufacturing Execution Systems (“MES”). In addition, TULIP digitizes formerly paper-based work procedure manuals, quality check sheets, and daily inspection to easily visualize and analyze production data, resulting in rapid process improvement.
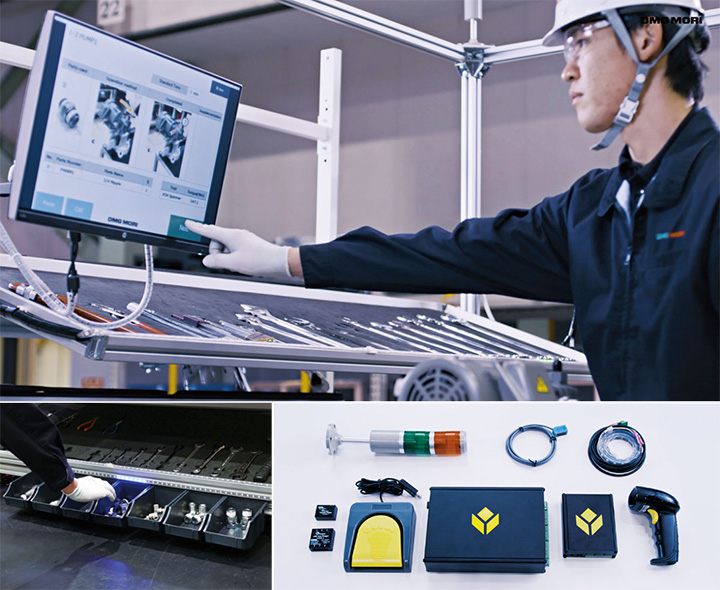
Engineering (Machining Technology)
Engineering (Machining Technology)
Significantly Reduced Production Lead Times and CO2 Emissions through Process Integration
Technology Cycles
Technology Cycles are solutions that make complex machining easier and faster. Machining, setup, and measurement, which used to be performed by specialized machines, programs, and cutting tools, can now be performed easily and with high quality by anyone using general-purpose machine tools and standard tools and fixtures.
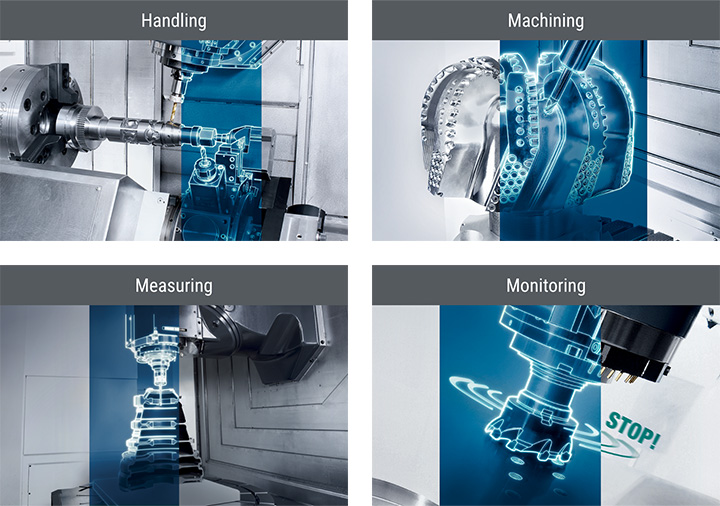
Technology Cycles
"Multi-Threading 2.0"
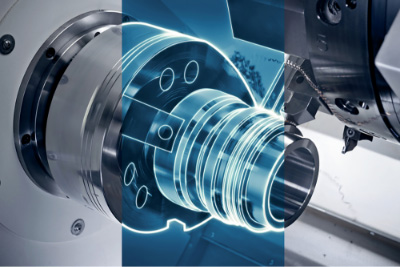
Worm gear machining with a general-purpose machine
- To machine special-shaped screw
- To simplify complex programming
Outcome (post-introduction)
- Various thread shapes to be easily created in an interactive format
- Machining programs for special shaped threads to be created on the machine without CAD/CAM
- Worms with involute curve tooth forms possible
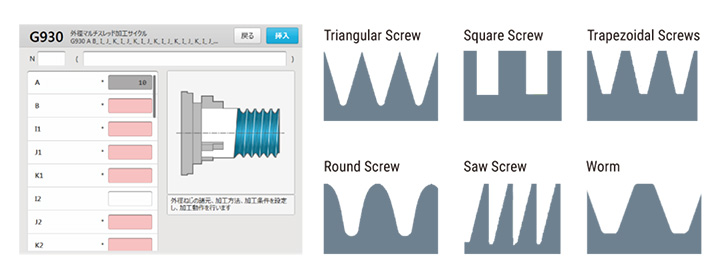
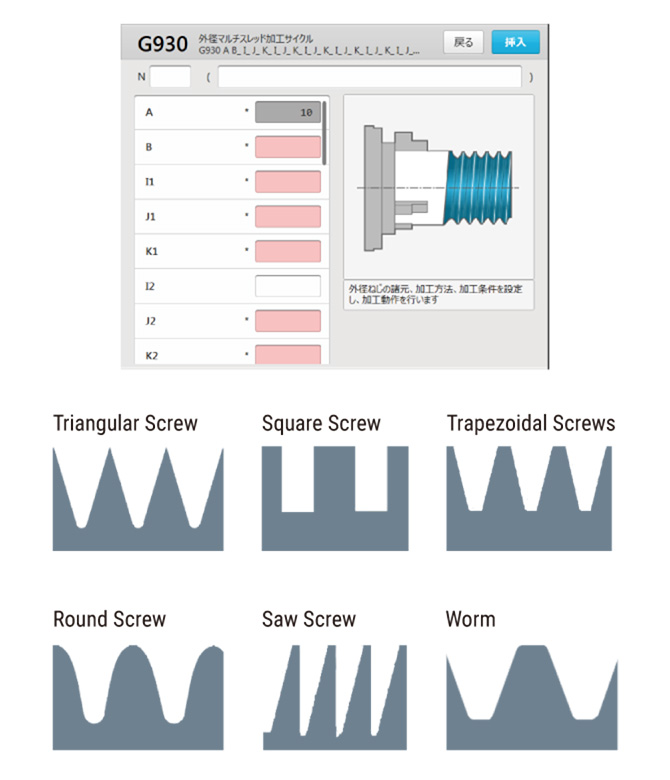