- トップページ
- DMG MORIの技術
DMG MORIの技術
DMG MORIは、社会的ニーズの大きな変化に応じて、技術を発展させ、提供する製品・サービスを進化させて成長してきました。
これからも社会のニーズに的確に対応した価値提供を通じて、さらなる成長を目指して参ります。
開発
イノベーティブな製品・技術により、
お客様価値の向上とカーボンニュートラルに貢献
Global Development Summit
(GDS/グローバル開発サミット)
Global Development Summit
(GDS/グローバル開発サミット)
日本、ドイツ、アメリカ、イタリア、ポーランドの開発拠点には計約1,300名の開発担当の社員が所属しています。
年に1度開催されるGDSでは、各拠点の担当者が直接顔を合わせて新技術開発について討議します。全体会合で今後の開発計画を確認した後、専門分野ごとの分科会にて、新技術やお客様の最新の動向などを具体的に検討・共有します。2020年、2021年はオンラインでの開催となりましたが、2022年は、11月に国内外から約100名の開発社員が東京に会合し、オンラインでも約200名が参加するハイブリッド形式での会議開催となり、部分的ではありますが3年ぶりの対面開催が実現しました。こうしたグローバルでの知の蓄積が当社の設計・開発の強みとなっています。
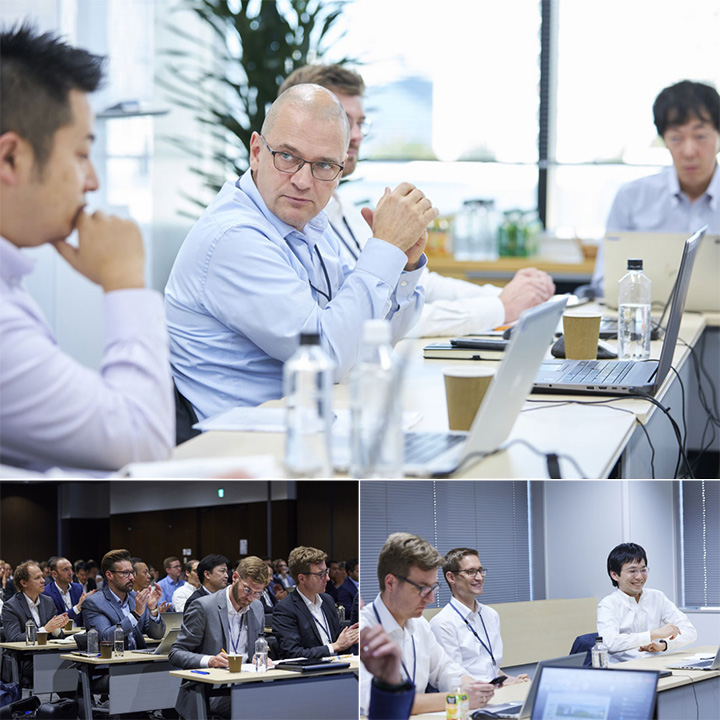
奈良商品開発センタ(奈良PDC)
奈良商品開発センタ(奈良PDC)
当社最大のデジタル・トランスフォーメーション(DX)構築と 先端技術の開発拠点となる「奈良商品開発センタ」を開設しました。
具体的には、次世代通信技術、AI(人工知能)、デジタルツインなどを活用したDX技術、次世代複合加工機の工作機械および周辺装置、ソフトウェアなどの開発を同センタで行っています。奈良PDCは、専用の開発実験センタを備えており、各大学や企業との産学連携も含め、工作機械及び周辺装置、それらに搭載される制御ソフトウェア等の最先端でイノベーティブな開発実験を行います。
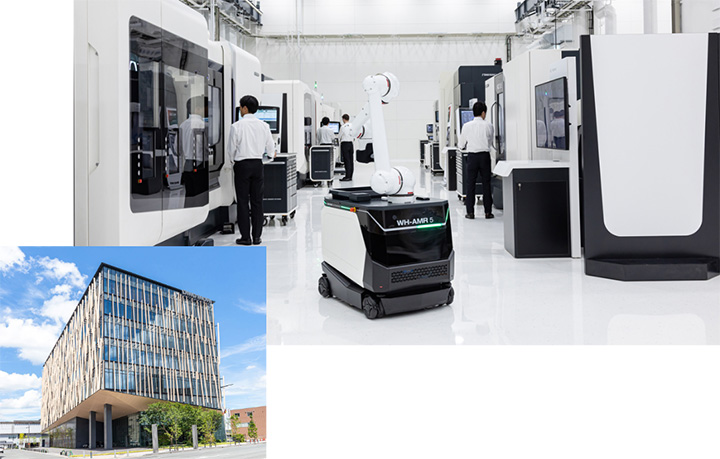
高精度加工と環境負荷低減の追求
高剛性・高精度による加工精度の向上と同時に、より環境負荷の小さい工作機械の開発を製品開発の基本方針としています。
一例として、2022年12月に高剛性と空間精度15μm以下の高精度を兼ね備えた大型横形マシニングセンタ「NHX 10000 µPrecision」を開発しました。同製品は、建設機械、航空機、金型、自動車、エネルギー産業など向けに大型ワー クの高精度加工を実現するとともに、従来機と比較した消費電力の削減により、お客様の環境対策にも貢献してまいりま す。今後も高度な部品加工ニーズに対応しつつ環境負荷を低減する製品の開発を通じて、GXの実現に貢献します。
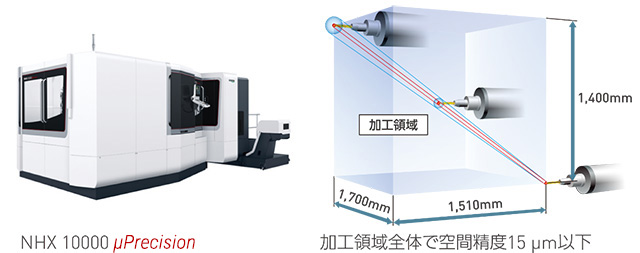
工程集約・カーボンニュートラル・サーキュラーエコノミーに
貢献するAM技術
アディティブマニュファクチャリング(以下、AM)技術は1986年に初めて特許化されてから目覚ましい発展を遂げています。
その途上において人々の興味は、試作を早める目的であるラピッドプロトタイピングから、機能試作を行うファンクショナルプロトタイピングへと変化しました。その後、新たな機能を付加する付加製造として、さまざまな業界に広まってきています。一から部品を作り上げるだけでなく、修理や補修の用途でも使用することが可能で、廃棄物や消費エネルギーの削減にも貢献しています。
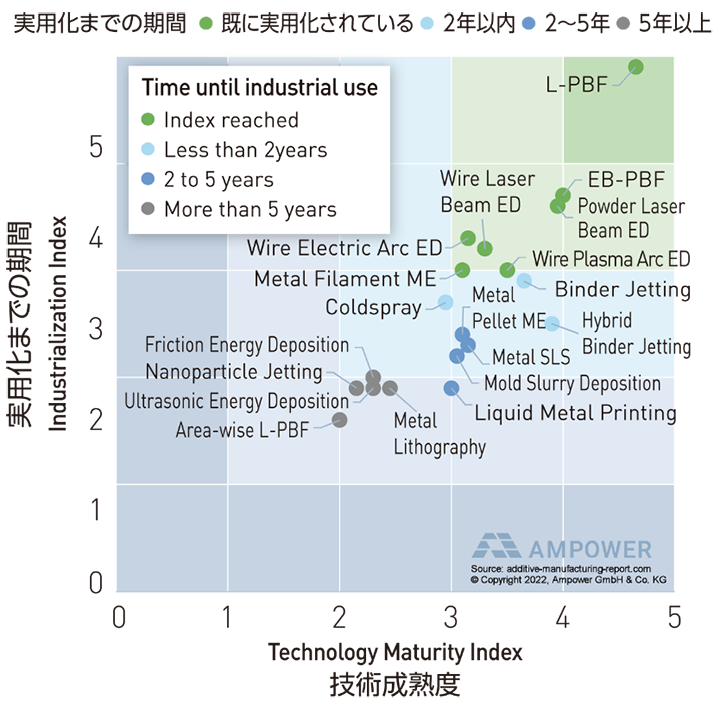
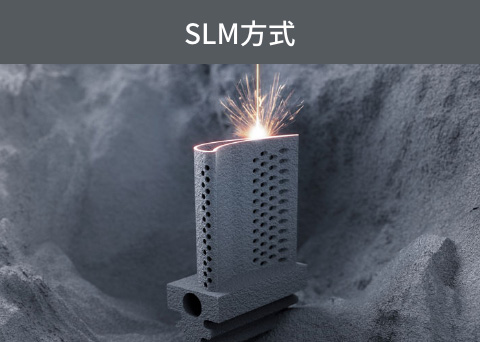
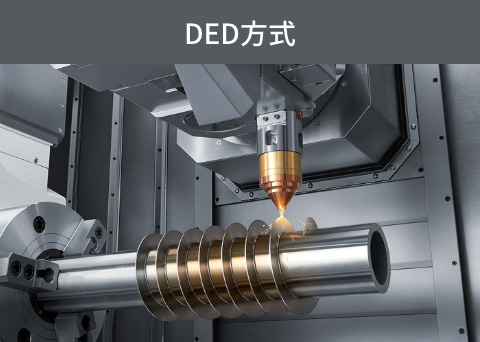
※実用化レベルと技術成熟度の関係はAMPOWER Report 2021のデータを参照
■ アディティブマニュファクチャリングDMG MORI受注推移
(全世界)
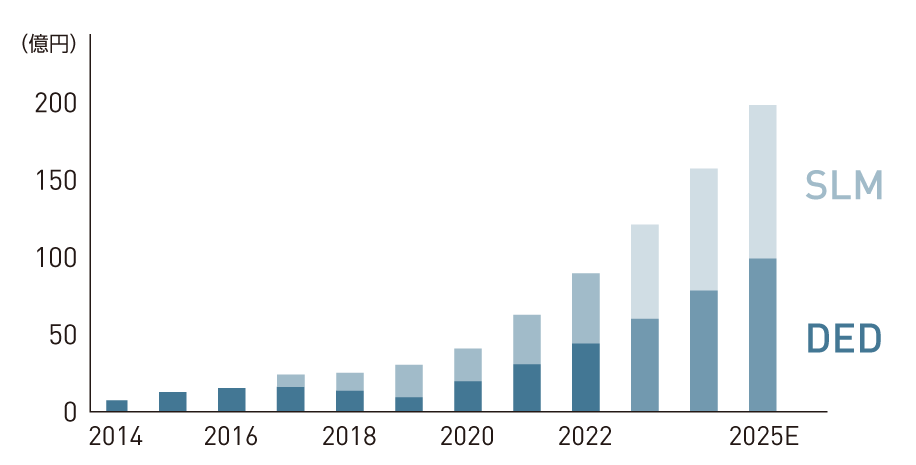
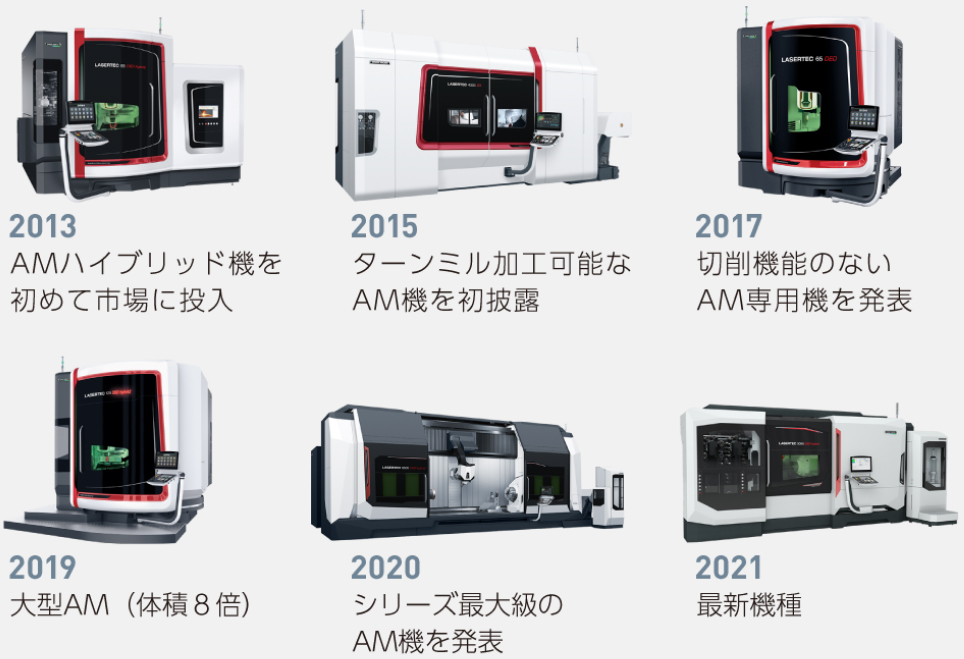
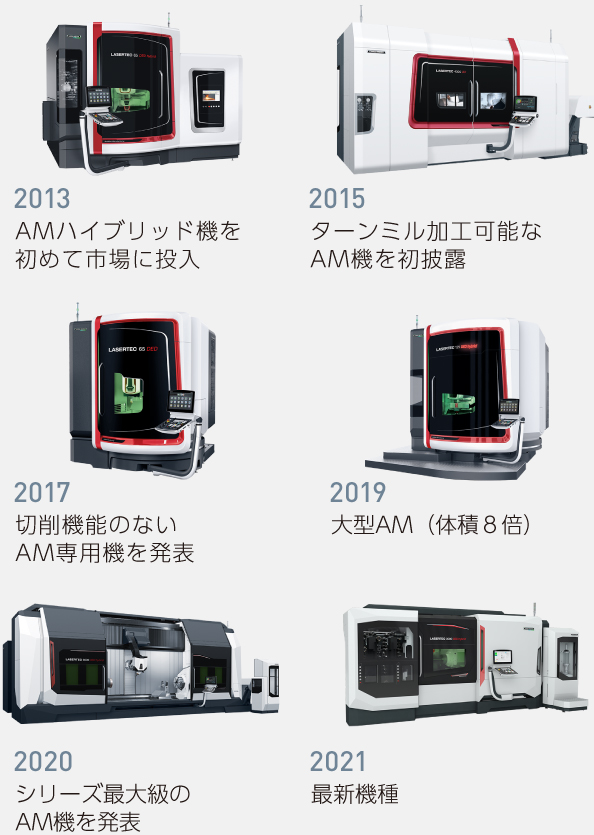
製造
高品質維持、安定供給、CO2 排出量削減に貢献
キーコンポーネンツの内製化
キーコンポーネンツの内製化
DMG MORIでは、品質向上と短納期化はもちろん、製品開発期間の短縮や安定供給などを目的に主要部品の内製化に取り組んでいます。ボールねじやATCをはじめ、部品加工から組立、検査までを一貫して行える主軸工場も重要な役割を果たしています。
内製化は、日本、ドイツほか、世界各地で進めています。
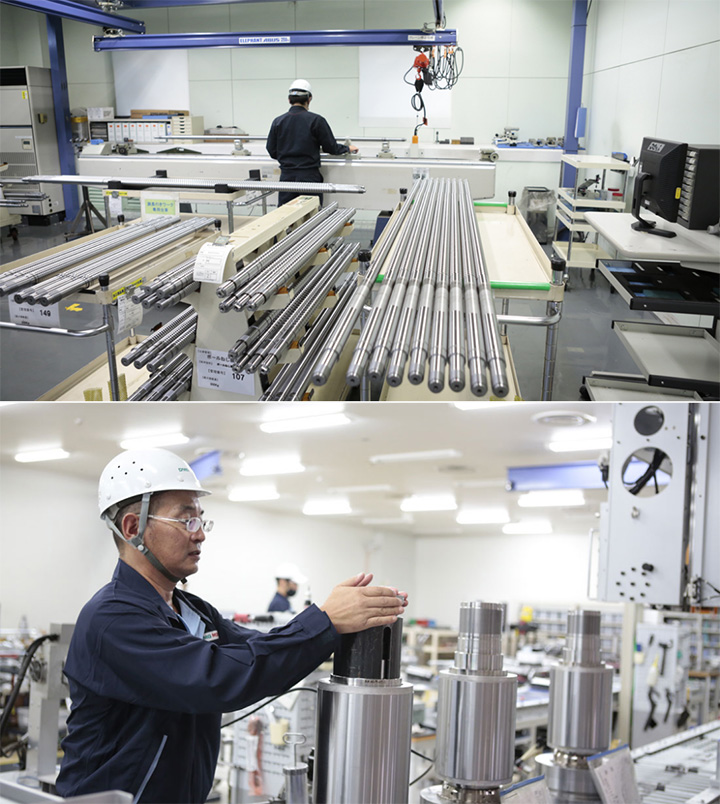
高性能主軸compactMASTER、
turnMASTERの新モデルを発売
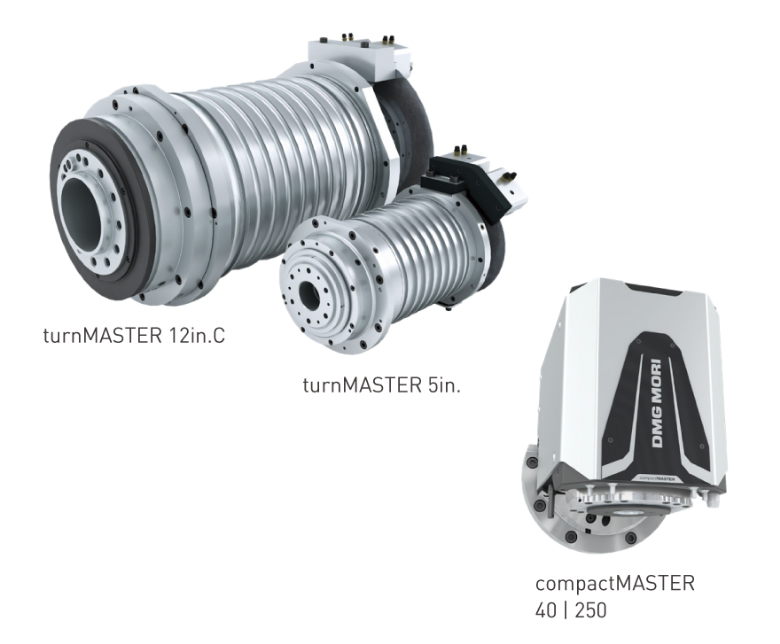
2022年6月に2種類の主軸を発売しました。一つは、ターンミル主軸「compactMASTER 40 | 250」で、全長250mmと世界最小クラスですが、高出力かつ最高回転速度42,000min-1の高速機能を有しています。
もう一つは、「turnMASTER 5in.」で、ターニングセンタや複合加工機に搭載される高精密、高性能主軸です。2023年2月には、ターニング用高性能主軸「turnMASTER 12in.C」(従来製品に比べて約18%スリム化を実現)を開発し、小型の工作機械に最大12インチのチャックの搭載を可能にしました。主要部品を内製化することで、多様な主軸の開発・生産をすることができます。また、品質に自信があり、無償保証期間を3年としています。
高速・高性能主軸を搭載し、サステナブルな体制で生産された工作機械を提供することで、お客様の生産の向上のみならず、CO2 排出量の削減などの環境に配慮した生産現場の実現にも貢献します。
製造現場のデジタル化
-TULIPをグローバル生産拠点に導入
製造現場のデジタル化
-TULIPをグローバル生産拠点に導入
製造支援アプリケーション作成プラットフォーム「TULIP」をDMG MORIの主要生産拠点に導入しています。TULIPにより、生産現場の担当者は、作業手順書、品質管理、機器のモニタリング、MES(Manufacturing Execution System)などを他のシステムとデータ連携するアプリケーションを作成することができます。また、紙の作業手順書、品質チェックシート、日常点検項目をデジタル化し、生産データの見える化・分析を容易にします。これにより、迅速な工程改善が可能となります。
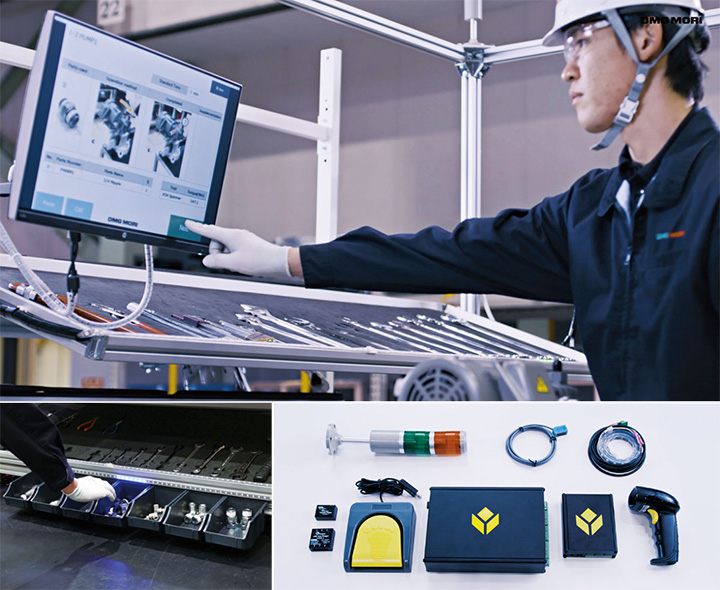
エンジニアリング(加工技術)
工程集約、自動化でお客様の生産性向上をサポート
DMG MORIテクノロジーサイクル
テクノロジーサイクルは複雑な加工を簡単かつ短時間で実現できるソリューションです。これまで専用機や専用プログラム、特殊な工具で行っていた加工・段取り・計測を、汎用的な工作機械や標準的な工具・治具などで、誰もが簡単かつ高品質で実現可能です。

テクノロジーサイクル
マルチスレッディング2.0
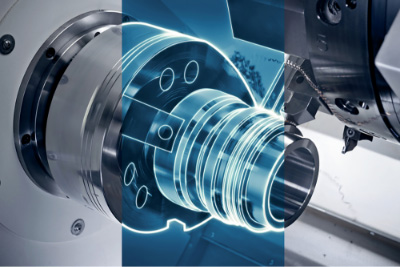
ウォームギア加工を汎用機で実現
- 特殊形状のねじを加工したい
- 複雑なプログラム作成を簡素化したい
成果(導入後)
- 対話形式で簡単に多様なねじ形状を作成
- 特殊形状ねじの加工プログラムをCAD / CAMなしに機上で作成
- インボリュート曲線の歯形をもつウォーム加工も可能
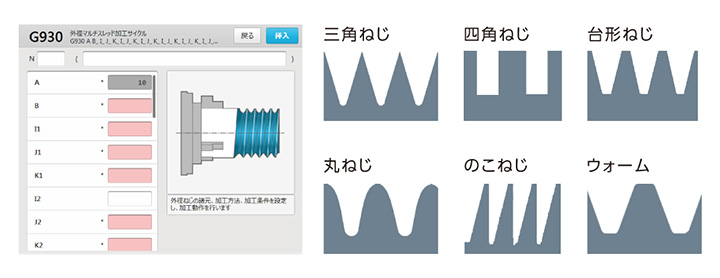
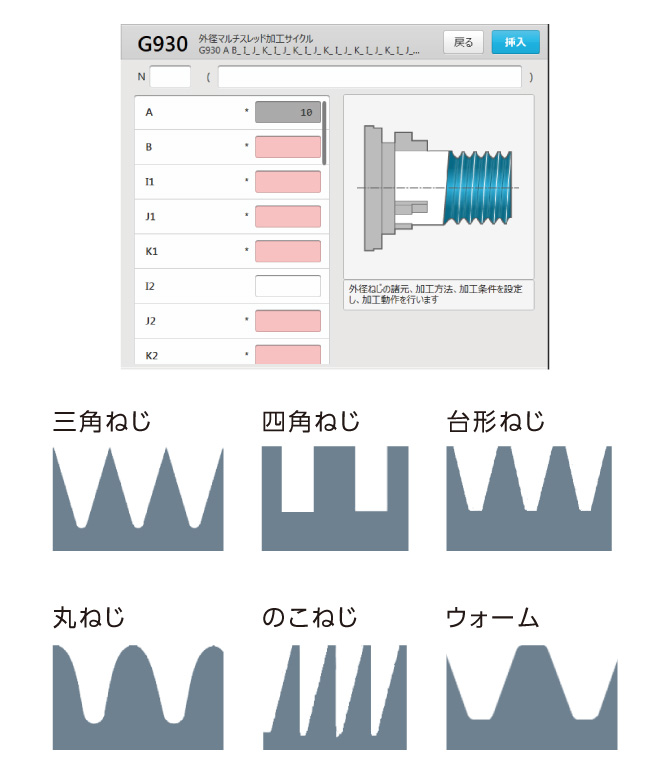