- Balita/mga paksa 2016/10/27 UP
-
Story behind the scene of developing the new machining center series “CMX V” by the person in charge of the product
- Tag
-
- Machining Centers
- Space-saving
DMG MORI unveiled the CMX V series models, new vertical machining centers at IMTS held in Chicago in September 2016 and began taking the order. The models will be showcased at JIMTOF 2016 for the first time in Japan and Asia.
The CMX V series was developed to answer to ever-diversifying and advanced needs of customers. The product concept is three “C”s that represent “Compact,” “Competitive,” and “Customized.” The machine name CMX derives from it.
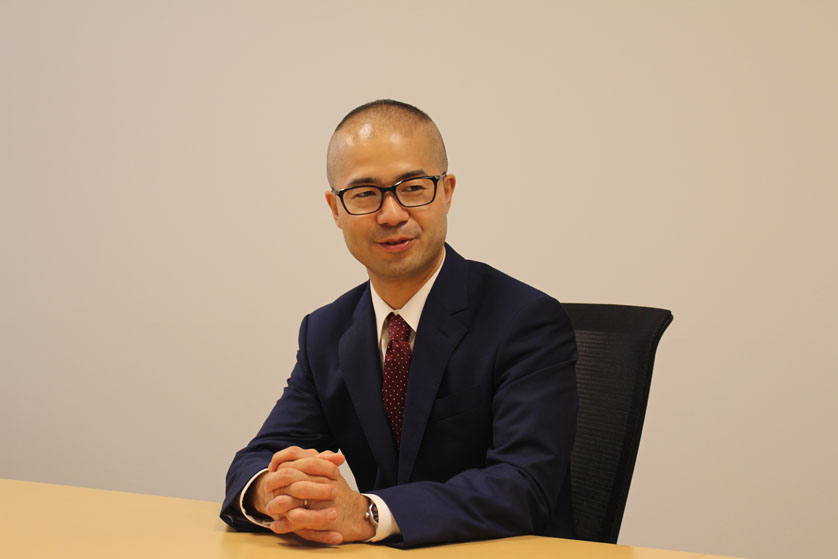
Takashi Yuasa, General Manager at the CMX/CLX Product Department
High added value created by customization
One of the most distinctive features of the series is that they are able to respond to a wide variety of customer demand with a total of 290 standard options. For example, the tool capacity of the magazine is 30 tools as standard, and 60 as an option. The maximum spindle speed is 12,000 min-1 as standard, and 15,000 min-1 as an option. DMG MORI positions the series models as its solution-based machines because of the flexible customization (special specification).
The cutting tools and peripheral equipment of our partners are employed as open innovation, and the series is compatible with “Technology Cycles,” which are DMG MORI’s new solutions that integrate machine bodies with embedded software and human-machine interface. Of all the “Technology Cycles,” six solutions including W setter are currently available for the series. Interpolation turning, MVC and MPC will also be available in the near future.
The Product Department that I belong to is located in the Iga Campus where the CMX V is developed and manufactured. The department sends updated product information to the Sales Department constantly, and the Sales sends back the customer feedback to us at the Iga Campus. We provide support so that more customers will be able to confidently choose our products as their best choices. Ever since I joined the company in 2001, I have been in charge of machining centers and feeling the evolution of machines firsthand. The CMX V series models are the new and first machines in the company that bring great added value with such varieties of options.
Making customers more competitive
One of the three “C”s in the CMX V represents our aspiration that the series will make the customer more “Competitive” in the industry. In the development of the series, we put a focus on functions, needless to say, and ease of use as a machine tool, which are “accessibility,” “operability,” and “visibility.” We especially devised various ways to achieve accessibility. Vertical machining centers are in many cases used for high-mix low-volume production, and accessibility to the table and spindle is a key to easy checking and replacement of tools.
It is rare for Japan-made machines that the spindle travels on the Y-axis like the CMX V. One of the drawbacks is that the Y-axis spindle is likely to vibrate when it reaches the front end. As a countermeasure, two supports (dual support) are attached to the column front face to firmly support the spindle movement on the Y-axis.
What’s more, the front cover line is dented towards the table side so that the operators’ foot can go a step closer to the table. The table height was thoroughly studied for the sake of operators’ comfort and good posture.
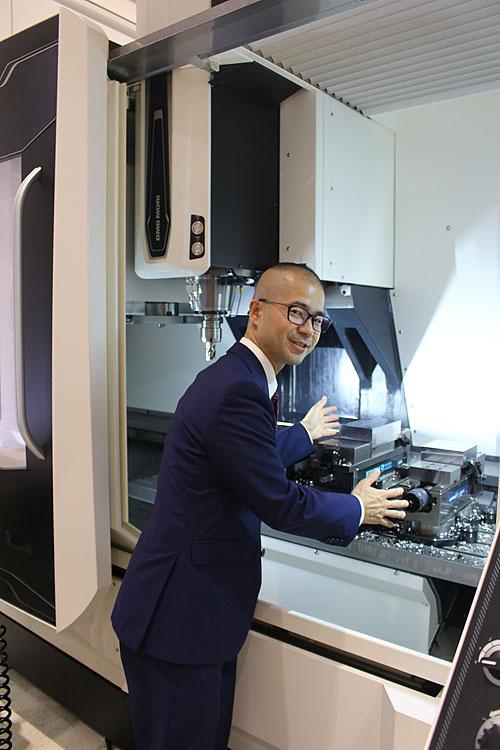
Front cover dented inward to ensure accessibility
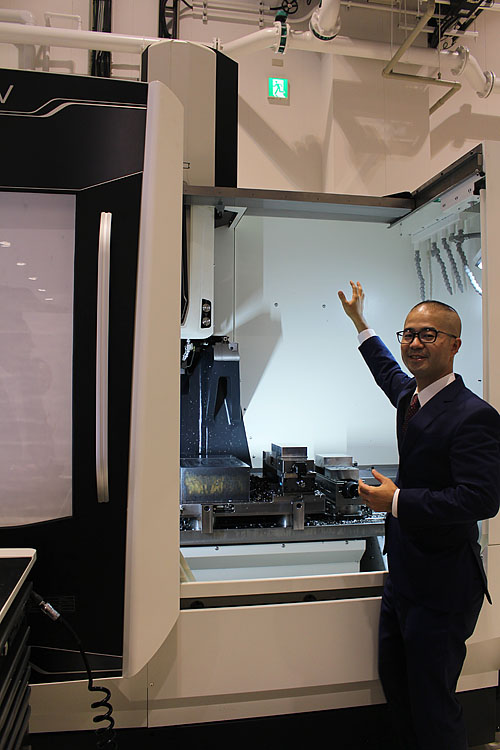
Automatic ceiling shutter for cranes
Delivery time as compact as machine size
Another “C” in the CMX V represents “Compact.” The series achieves the Y-axis travel of 560 mm, the largest in its class, while being a compact body. The series models are equipped with the automatic ceiling shutter so that a crane can load/unload large and heavy workpieces from the ceiling, which ensures outstanding space efficiency.
Functions of the robot system which are currently under development at our Transfer Technology Department has been modularized, and they will be available for the CMX V series as peripheral equipment options.
The already designed and modularized units such as a workpiece stocker, a workpiece turnover unit and a deburring unit can be flexibly combined like a piece of a puzzle according to customer demand. This allows for shorter delivery times compared to the process that we have to start with a meeting on a machine design with customers. The shop floor layout also can be easily changed in accordance with their workpieces. We make much of customers’ perspective when modularizing each unit. Fixtures are, for example, usually designed after workpieces have been determined, but we can achieve both shorter delivery times and higher quality by doing in-depth analysis on customers’ workpieces in advance and prepare the fixtures appropriate for them.
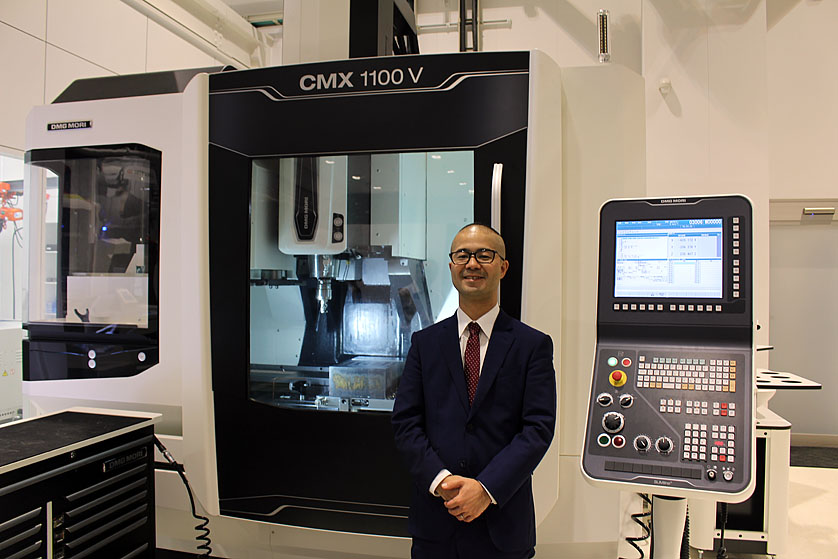
Final message for customers
The biggest feature of the CMX V is “Customization.” We are committed to being a provider of solutions to any troublesome issues of customers with a passion of “taking care of everything for them.” So don’t bother picking everything necessary for machine installation. Please contact us and let us support you!