DMG MORI Gear Cutting Solutions
Realize gear cutting on your existing machines
with DMG MORI Technology Cycles.
Why not use your existing machines for gear production?
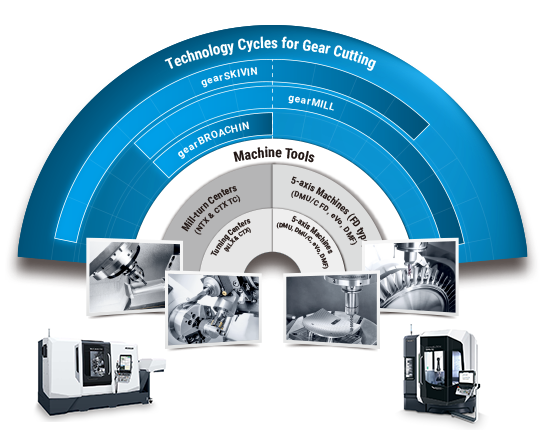
Have you ever faced the need for gear machining but were unable to perform specialized processes, such as internal gear cutting? In such cases, your options were likely limited to declining the request or outsourcing the production.
Now, DMG MORI offers the perfect solution to these challenges. With our Technology Cycles, you can seamlessly perform gear machining on your existing machines!
Benefits of DMG MORI Technology Cycles
- Speed : Input gear parameters quickly through a guided menu.
- Simplicity : NC programs are automatically generated based on the input gear parameters.
- Retrofit : Upgrade your existing machines to handle the latest machining processes.
DMG MORI Gear Cutting Solutions
Create NC programs by
entering gear parameters through interactive guidance.
- A Complete Set of 65 DMG MORI Technology Cycles
– Simple Solutions for Complex Machining -
ー Cutting Cycles (26 types)
Technology Cycles to realize new machining methods, such as gear machining on universal machines
ー Handling Cycles (18 types)
Technology Cycles to support machine operation and setup
ー Measuring cycles (11 types)
Technology Cycles to support measurement work
ー Monitoring cycles (10 types)
Technology Cycles for preventive maintenance by monitoring of machine operation, tool load, etc.
- Up to 60% faster programming through
interactive guidance -
DMG MORI Technology Cycles support customers create programs that unlock the full potential of their machines, achieving maximum productivity.
- ー Easy-to-understand program structure
- ー Up to 60% faster programming
- ー Interactive dialog-based programming to reduce input errors
- ー Achieve gear machining and grinding on existing machines
- ー Self-made programs are stored as internal know-how
- ー Guided input of gear parameters for NC programming
Technology Cycles for gear cutting
gearSKIVING- Skiving for inner and outer diameters up to 11 mm modules
gearMILL- Gear machining for modules of 3 mm or larger using standard universal tools
gearBROACHING- Broaching operations for inner and outer diameters up to 4 mm modules
safeRETREAT- Allows tool and workpiece to retreat safely by pushing the emergency stop button
Multi-Threading 2.0- Programming support for special thread machining
gearHONING- Honing for mill-turn centers
gearHOBBING- Supports gear machining with hob cutters
gearSHAPING- Supports gear shaper programming for special-shaped spur gears and internal gears
gearQUALITY- Non-contact on-machine measuring by laser scanner
DMG MORI Technology Cycles
gearSKIVING
— High-speed gear machining, incl. internal gears
- Main features
- + Easily use "gear skiving" - an innovative method for gear machining by synchronously rotating workpiece and skiving tool at a constant angle
- + Supports machining of internal gears, which cannot be achieved by hobbing
- + Process integration on a single universal machine eliminates workpiece transfers and reduces setup errors and setup time
External gear machining
Dialog-based input of necessary gear data
Internal gear machining
Automatic NC program creation
- Compatible models
- Max. turning diameter*1
- NLX / CTX
(Y-axis type) - 150 mm
- NTX 1000 /
CTX beta TC - 340 mm
- NTX 3000 /
CTX gamma TC - 500 mm / 530 mm
- DMU eVo / DMF
- 800 mm
- DMU / DMC FD monoBLOCK
DMU / DMC FD duoBLOCK
DMU / DMC FD Portal - 3,200 mm
*1 Availability depends on gear type and machine specification.
DMG MORI Technology Cycles
gearMILL
— Gear machining with universal machines & standard tools
- Main features
- + PC software for gear machining
- + Full process integration enabling turning, milling, and gear machining on a single machine
- + Uses conventional tools and universal machines, reducing costs for investment in specialized equipment
Simply input the gear parameters to generate an NC program. Also supports CAM post-processing and simulation.
A non-contact, on-machine measurement system*2 that uses sensing technology to automatically measure workpieces directly on machine tools. It enables high-speed and high-precision measurements.
- Compatible models
- Max. turning diameter*3
- NTX 1000 /
CTX beta TC - 500 mm
- NTX 3000 /
CTX gamma TC - 670 mm / 700 mm
- DMU eVo / DMF
- 800 mm
- DMU / DMC monoBLOCK
- 1,000 mm
- DMU / DMC duoBLOCK
DMU / DMC Portal - 3,200 mm
*2 Available for DMU / DMC series (monoBLOCK, duoBLOCK, eVo).
*3 Availability depends on number of teeth, tool size, and machine specification.
DMG MORI Technology Cycles
gearBROACHING
— Achieving gear broaching on mill-turn centers
- Main features
- + Supports gear broaching for both internal and external diameters
- + Corrects tool holder deflection
- + Compatible with machines equipped with SIEMENS controllers
Define tool parameters
Automatic adjustment of tool displacement
- Compatible models
- Max. turning diameter*4
- NTX 1000*5 /
CTX beta TC - 500 mm
- DMU / DMC duoBLOCK
DMU / DMC Portal - 670 mm / 700 mm
*4 Availability depends on number of teeth, tool size, and machine specification.
*5 Only for SIEMENS specification.
DMG MORI Technology Cycles
safeRETREAT
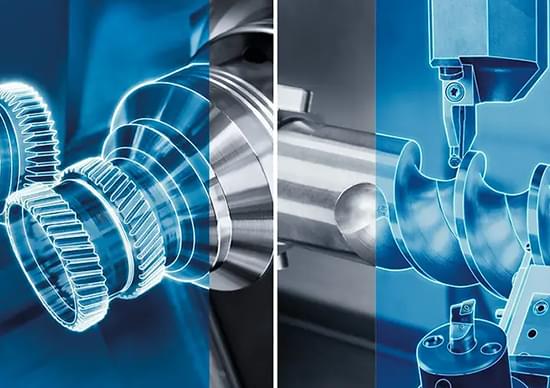
- Main features
- + Safely retracts the tool and workpiece with a single press of the emergency stop button
- + Protects the tool and workpiece from damage in unexpected situations
- + Available as an additional option for gearSKIVING 2.0 and Multi-Threading 2.0.
Switching safeRETREAT on and off in gearSKIVING 2.0.
Switching safeRETREAT on and off in Multi-Threading 2.0.
- Compatible models
- CTX TC, CTX TC 4A
DMG MORI Technology Cycles
Multi-Threading 2.0
- Main features
- + Supports threading at specified positions
- + Allows customizable thread shape, pitch, and number of starts
- + Capable of machining large threads for gearboxes, which are beyond the scope of standard threading methods
Input parameters for thread length, thread position, and retraction distance.
Parameter settings for thread shape (e.g., thread height, pitch circle diameter, etc.).
- Compatible models
- NEF, CTX, NLX, NZX (with tailstock), CLX TC, CTX TC, CTX TC 4A, NTX, NT, SPRINT 50 / 65, NZX、CTX 4A, ALX, ALC, CTX TC*, CLX TC*, LASERTEC 3000 DED hybrid
*Included as standard function
DMG MORI Technology Cycles
gearHONING
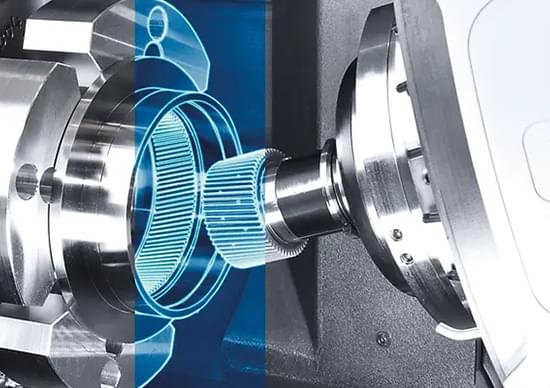
- Main features
- + Designed to perfectly complement gear skiving on mill-turn centers
- + Centralized setup on the control panel, incl. automatic tooth surface measurement
- + Technical support from DMQP partners, covering everything from tool design to machining
Parameter settings for probe measurement between gear teeth
After skiving operation
After honing operation
- Compatible models
- CTX TC, CTX TC 4A
DMG MORI Technology Cycles
gearHOBBING
- Main features
- + Interactive gear parameter input for easy programming
- + Supports machining of spur gears, helical gears, and worm gears
- + Compatible with hob cutters and disc cutters
- + Adjustable cutter position to maximize tool life
- + Achieves DIN 7-grade gear accuracy
Interactive input of all gear data
Input of gear parameters for single-tooth or single-groove machining
- Compatible models
- CTX*, NLX, CLX TC, CTX TC, CTX TC 4A, NTX, NT, SPRINT 50 / 65*, NZX, CTX 4A, ALX, ALC, DMU eVo, LASERTEC 3000 DED hybrid
*Y-axis specification required
DMG MORI Technology Cycles
gearSHAPING
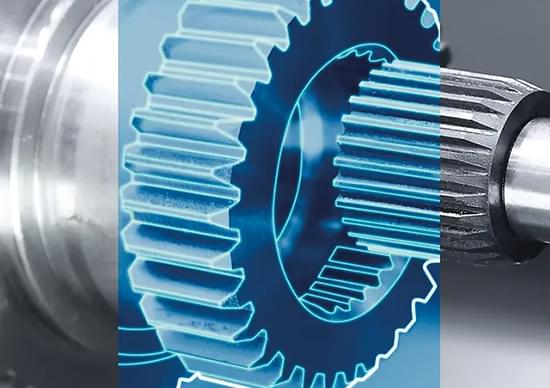
- Main features
- + Supports machining of spur gears and internal gears with shoulders (interference contours)
- + Achieves gear machining quality of grade 8 per DIN3961, supporting gear modules from 0.3 to 1.5 mm
- + On CTX gamma TC*, supports modules up to 2 mm
- * Machining quality and time may vary depending on the tool and workpiece.
Parameter input screen for external gears
Parameter input screen for internal gears
- Compatible models
- CTX TC, CTX TC 4A, DMU / DMC monoBLOCK
DMG MORI Technology Cycles
gearQUALITY
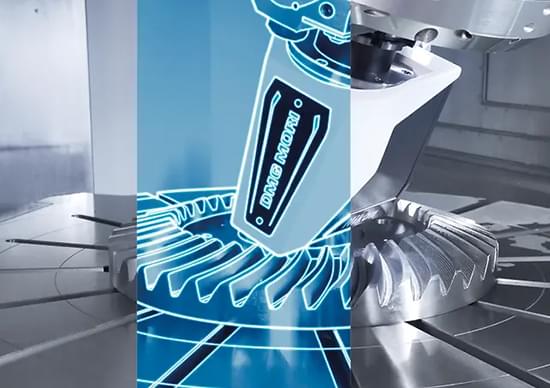
- Main features
- + Non-contact measurement using a laser scanner
- + Gear measurement and evaluation based on standards equivalent to 3D measuring machines
- + Captures point cloud data at 70,000 or 200,000 points per second, depending on the laser scanner
Simulation of the generated measurement program
Graphic visualization of shape deviations from design data
- Compatible models
- DMU / DMC duoBLOCK
Non-contact on-machine measuring system
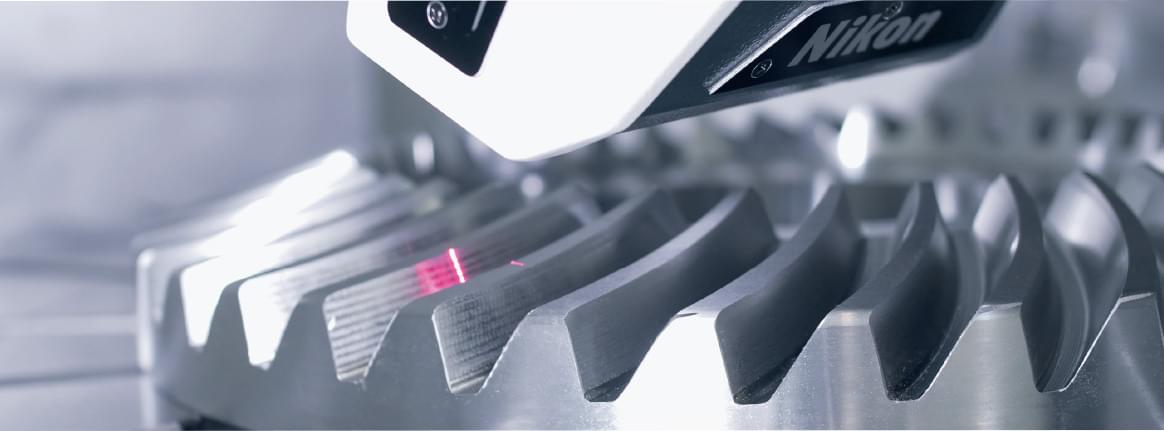
- Reduced measurement time
- + Measurements can be performed directly on the machine tool, eliminating the need to transfer to a dedicated measuring device
- + Two types of laser scanners capable of capturing 70,000 or 200,000 points per second enable rapid measurement
- + Efficiently measures large and complex workpieces, such as large gears or turbine blades, in a short time
- High-precision measurement
- + Surface-based measurement reduces measurement time and provides higher measurement accuracy.
- + Measurement accuracy equivalent to that of dedicated machine is achieved by DMG MORI's spindle control technology and measurement know-how of a measurement manufacturer.
- + Specialized workpiece measurement evaluation software automatically evaluates measurement results
- Easy measuring
- + Simply attach the laser scanner to the spindle of your machine tool to begin use immediately
- + Can be implemented at roughly 1/5 the cost of a dedicated measuring machine*6
- + Measures point clouds at micrometer-level accuracy using laser projection
- + Measurement results are instantly displayed on a computer
- + Captures shape data instead of just workpiece dimensions, allowing overlay comparisons with CAD drawings
- *6 Based on our research, calculated as a price comparison to the implementation cost of large gear measuring machines.
- Gear-specific evaluation and analysis
- + Compare and analyze design data while visualizing full tooth surface shape deviations with graphics
- + Supports various gear types, incl. cylindrical gears (internal/external), bevel gears (straight bevel, spiral bevel, and hypoid gears)
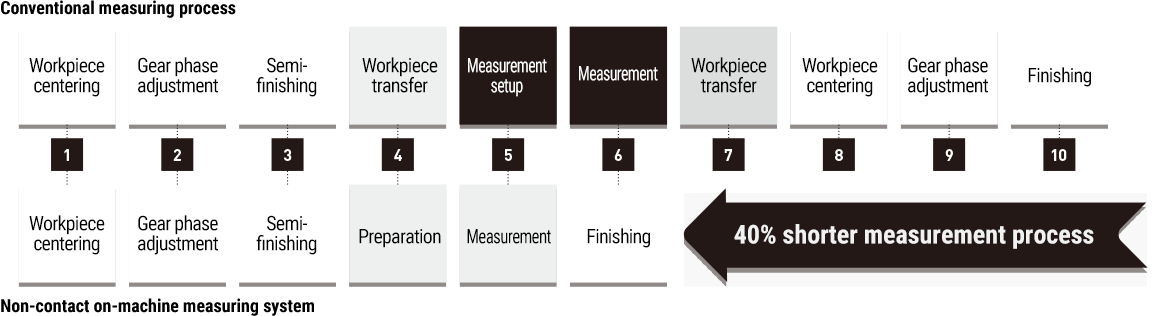
Measurement Comparison for Helical Gears (φ 300 mm / 73 Teeth)
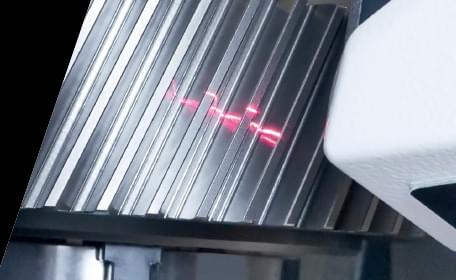
CMM 40 min |
Non-contact on-machine measuring system 13 min |
|||
---|---|---|---|---|
Gear phase adjustment | 20 min (manual) | 3 min (automatic) | ||
4 teeth | 7 min | 4 min | ||
Deviation adjustment | 13 min | 6 min |
Gear Solution Gear Production+
5-axis machine equipped with a gear grinding unit
for integrated milling, turning, gear roughing and grinding
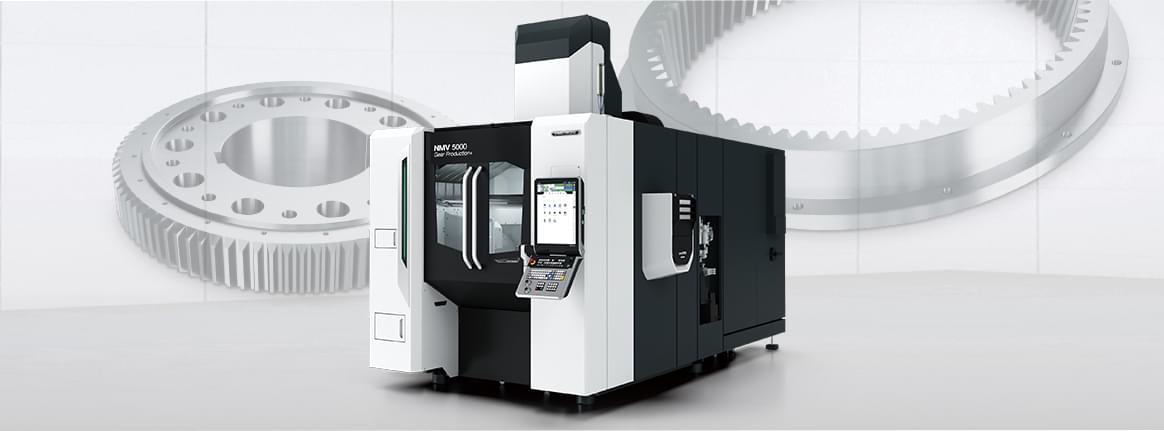
Gear Production+ by NMV 5000 DCG
For various types of industrial gears
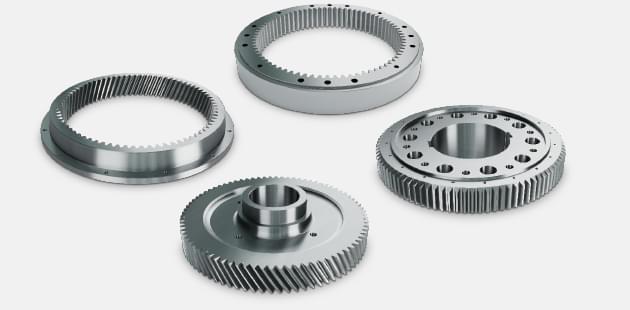
- + Module: m2 - m6
- + External gears: up to φ400 mm
- + Internal gears: φ120 to φ430 mm
Also handles groove shapes like splines and keyways.
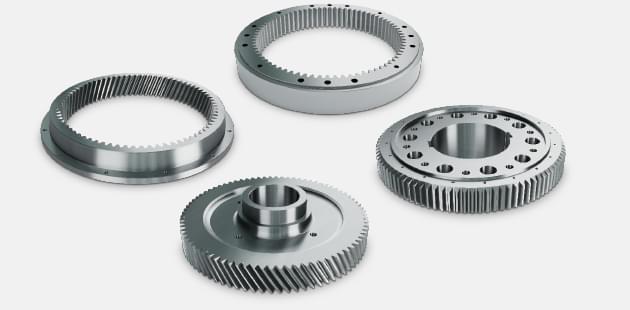
Accuracy measurement results
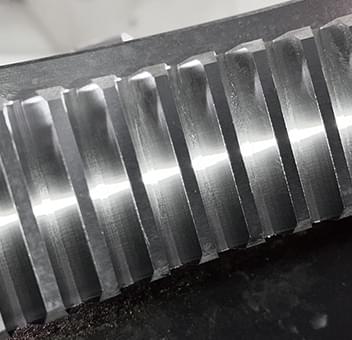
Measured values | Workpiece specifications | |||
---|---|---|---|---|
Tooth profile error | ISO Grade 4 | Module | 2.5 (mm) <0.10 (in.)> | |
Tooth trace error | ISO Grade 4 | Number of teeth | 84 | |
Pitch error | ISO Grade 4 | Pressure angle | 20 (deg) | |
Tooth groove runout | ISO Grade 4 | Material | S45C (High-frequency hardened) |
Gear Grinding Unit
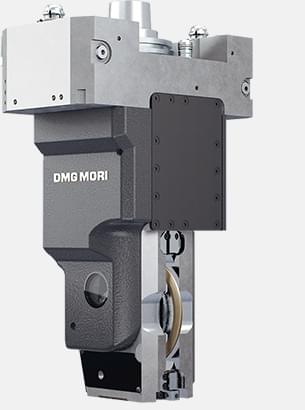
- In-machine stocker
The gear grinding unit is stored in a dedicated in-machine stocker. Automatic tool change enables roughing and grinding in one machine.
- Tooth alignment function
The tooth phase alignment function automatically detects the gear phase during roughing for stable grinding allowance and shorter processing time.
Reduced machining time through process integration
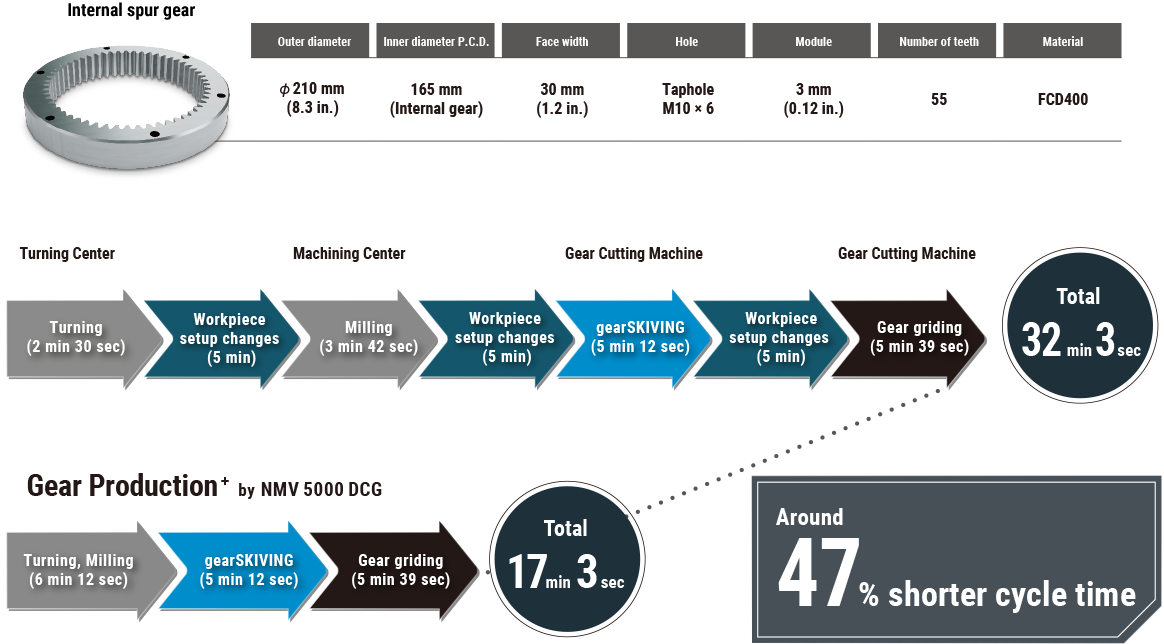